The pharmaceutical industry (and other regulated sectors) operate under strict adherence to specific standards and regulations. One of the most critical of these standards is the Current Good Manufacturing Practice (cGMP). These guidelines are used as a means to validate the quality, consistency, and safety of drugs, ensuring that they serve their intended use, without causing harm. As technology evolves, companies are leveraging laboratory control systems to ensure they meet these requirements.
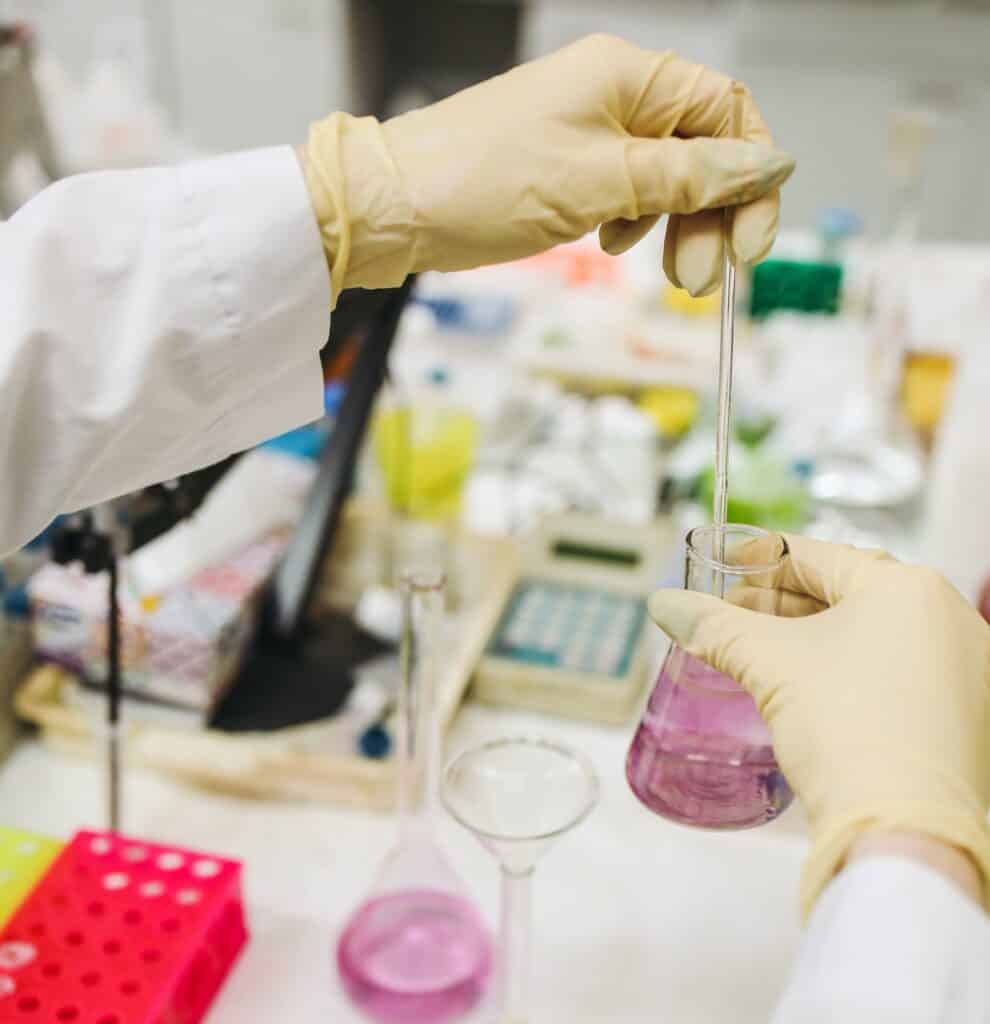
Understanding cGMP Standards
cGMPs are regulatory guidelines that provide the framework for drug product quality assurance. They ensure that drugs meet the necessary quality and purity standards, free from contamination, and consistent in their intended use. While these standards have existed for a long time, recent technological advancements, especially in laboratory control systems, have made compliance more straightforward and efficient.
The Role of Laboratory Control Systems
Modern laboratory control systems have transformed how pharmaceutical companies approach cGMP compliance. These systems, which integrate seamlessly with existing laboratory equipment and protocols, provide the following advantages:
- Automated Data Collection: Manual record-keeping is prone to errors. Automated systems ensure accurate and timely data capture, reducing the likelihood of mistakes and inconsistencies.
- Traceability: With a laboratory control system, every step of the manufacturing and testing process is tracked and recorded. This traceability ensures that should any quality issues arise, the source of the problem can be quickly identified and rectified.
- Enhanced Security: These systems are equipped with advanced security features that protect sensitive data from unauthorized access, ensuring that only designated personnel can access or modify records.
- Efficient Reporting: Automated systems allow for quicker generation of reports by facilitating timely reviews and applying a swift decision-making process.
- Scalability: As a company grows, its control systems can adapt, ensuring that regardless of the volume of production or testing, cGMP requirements remain consistently met.
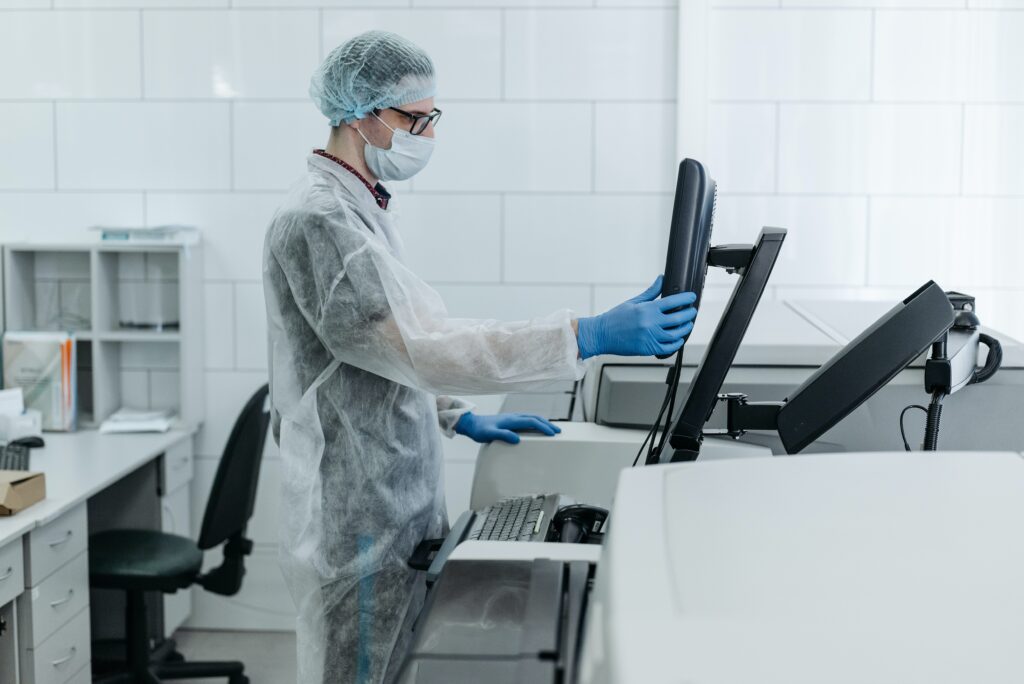
Challenges and Solutions
While implementing a laboratory control system offers numerous advantages, it’s essential to be aware of the potential challenges. Some of these include:
- Integration with Existing Systems: Not all laboratory equipment is compatible with new control systems. However, most modern systems are designed to be adaptable and can be customized to integrate seamlessly with existing infrastructure.
- Training: Transitioning from manual to automated processes requires personnel training. The key is to provide comprehensive training sessions, ensuring that everyone understands the nuances of the new system for seamless integration.
- Maintenance: Like any other system, laboratory control systems require regular maintenance – however, the benefits in terms of time savings and errors reduction far outweigh the occasional need for system updates or fixes.
A More Digital Future
As the pharmaceutical industry moves towards a more digital future, laboratory control systems play a pivotal role in ensuring that companies remain compliant with cGMP requirements. Through automation, enhanced security, and efficient reporting, these systems pave the way for safer, higher-quality drug production.
Are you ready to experience the pinnacle of quality and compliance in manufacturing?
Discover the Gold Standard in cGMP Operations: At Novex, we take pride in our unwavering commitment to Current Good Manufacturing Practice (cGMP) standards. Our dedicated team of experts meticulously oversee every aspect of the production journey, ensuring your peace of mind and product excellence.
Learn more about how to elevate your cGMP manufacturing standards today.